Category: Rubber Molds FAQs
What is an injection mold?
A rubber molding die specially used for rubber injection vulcanizing machines, called a rubber injection mold.
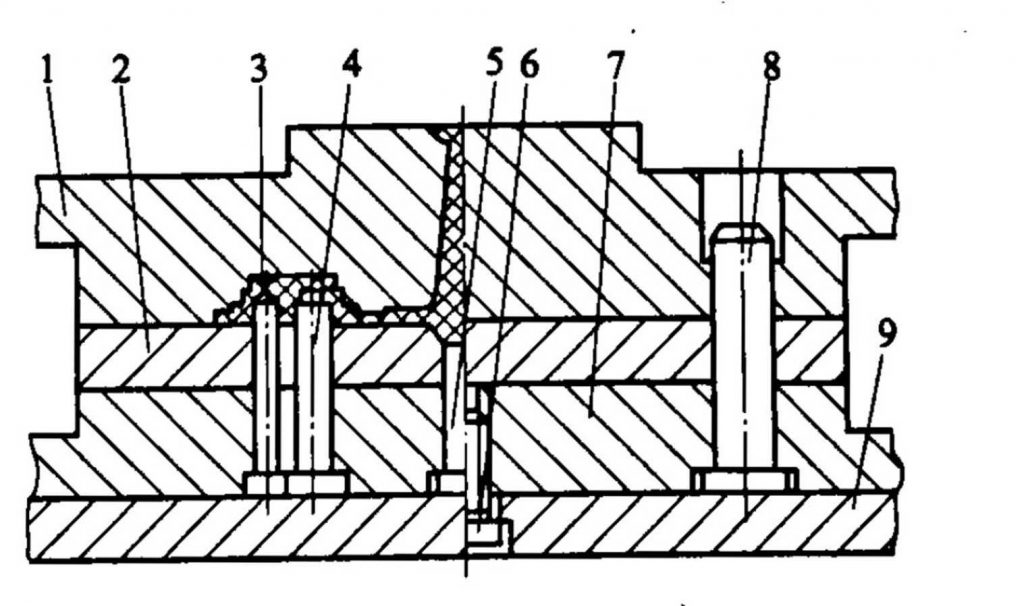
The rubber injection mold and the plastic injection mold are basically the same in structure, and the rubber injection mold is also referred to as an injection mold. The mold is made of special injection molding equipment (such as screw injection machine, screw plunger injection machine, rotary injection machine, etc., these injection molding equipment are equipped with a clamping mechanism), which will preheat the plasticized state of the rubber compound ( The preheating device on the injection machine forcibly squeezes the injection into the mold cavity, and then vulcanizes and molds to obtain the product parts. The basic structure of the rubber injection mold is mainly composed of fixed mold and dynamic mold. The rubber material enters the cavity from the nozzle of the injection machine through the fixed flow path system, and the moving mold follows the moving template to complete the opening and closing action, and most of them have automatic items. Out of the device.
The injection mold is the same as the injection mold. It is closed and re-injected. It also has the advantages of less rubber edge and good quality, and has high production efficiency and automation. However, the structure is complicated and the cost is high. It is only suitable for mass production. Products.
What is a die casting mold?
A rubber molding die specially used for rubber die casting vulcanizers, called a rubber die casting mold.
The die-casting mold (ie, rubber die-casting mold) can be divided into two-plate structure (mainly composed of upper template and lower template), three-plate structure (ie, upper mold, middle mold, lower mold) and lower top type. Demolding structure, side-supporting demolding structure, flattening and demolding structure, side core-pulling structure and vacuuming structure.
The common feature of die-casting molds and self-pressing injection molds is that both have their own flow path system. The die-casting mechanism of the die-casting mold is owned by the rubber die-casting vulcanizing machine, and the injection mechanism of the self-injecting mold is the mold itself. In addition, the die-casting mold is of a fixed type [the upper die plate is fixed to the boom (neutron) on both sides of the rubber die-casting machine, and the lower die plate is fixed on the lower heat plate], and the self-pressing die is a mobile structure.
Die-casting molds are highly automated or semi-automated in rubber molding production, with low operating labor intensity, high production efficiency, and easy product quality.
What are the characteristics of the injection mold?
The injection mold is also called a self-pressure injection mold or a die-cast mold.
The injection mold can be divided into two types according to the structure, one is a separate structure (combined injection mold), and the other is a one-piece structure (integral injection mold).
The separate injection molding die is also called a combined injection molding die. When using such a mold, the mold should be clamped first (if the product part contains a skeleton, the skeleton is first installed or fixed in the mold cavity), and then the injection device equipped with the quantitative compound (ie, the hopper and the plunger) Place it in the center of the plane on the mold or in the proper position, then start the vulcanizer pressure system. At this point, the rubber will pass through the plunger to take the pressure from the hot plate of the vulcanizer, and plastically deform and flow. Through the flow channel system of the mold, it is forcibly squeezed into the cavity of the mold. After the rubber is filled into the cavity, the hot plate of the vulcanizer is returned, the injector is taken out, and the mold is repressurized and heated. After the vulcanization time specified by the process is reached, the mold can be taken.
Integral injection molding, the structural feature of this type of injection mold is that the mold itself is compatible with the structural elements of the injector (hopper and plunger). The mold has a special feeding chamber and a flow passage leading to the cavity, and the rubber in the feeding chamber is pressed into the cavity through the flow passage under the pressure of the plunger. These molds are strong in overall structure, compact in structure, easy to use, and have high production efficiency.
The characteristic of the injection mold is that the cavity is closed first and then injected into the rubber compound, so the rubber edge is less, and the rubber material is injected through the flow passage under a higher pressure, so that the gas is sequentially discharged according to the advancement of the rubber material, and the rubber material flows through the flow. After the road becomes more uniform, the temperature of the rubber compound is increased, so the quality of the product is high, especially the large-sized rubber-inlaid metal insert products with complicated shapes, which are suitable for injection molding, and can inject thin wall which cannot be manufactured by ordinary compression molding. , super long and super thick products. Sometimes the injection mold has an ejection device to facilitate the removal of the product while also improving the efficiency and the life of the mold.
Injection molding is generally used in the manufacture of parts with complex shapes or rubber parts containing skeletons. The structure of the mold is complicated and the manufacturing cycle is long. However, with the popularization and application of digital controlled boring machines, machining centers and CNC engraving machines, the processing becomes more and more simple.
What are the characteristics of the semi-closed filling die?
From the structural point of view, the semi-closed filling die combines the advantages of an open filling die and a closed filling die.
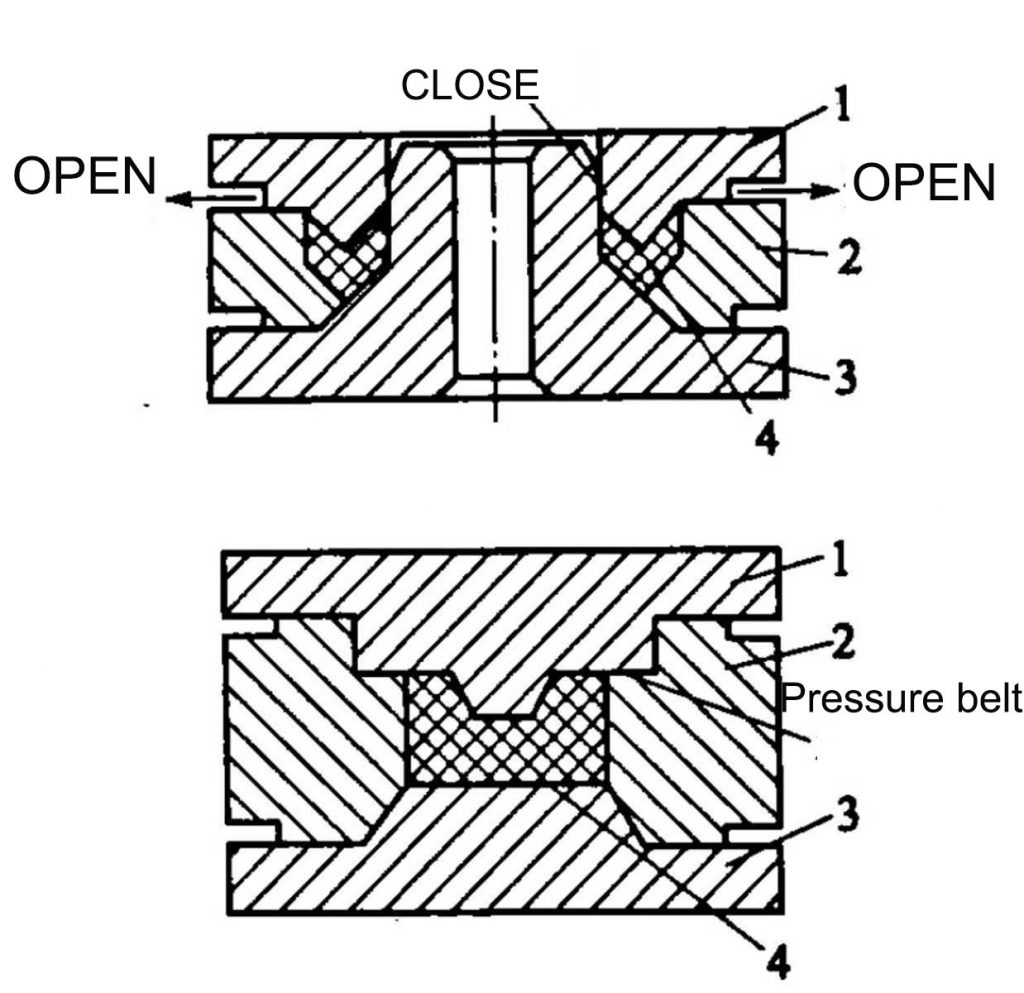
From the structural point of view, the semi-closed filling die combines the advantages of an open filling die and a closed filling die.
The figure above shows a semi-closed V-ring seal. It can be seen that the inner ring of the V-ring die is closed first, similar to the closed type, while the other side (outer ring) is open and open, until The stamper is closed when it is completely closed. This structure, which has both a closed portion and an open portion, is called a semi-closed type.
The continuation of the mold cavity is larger than the cavity. At this time, the pressure of the press is pressed on the rubber, and a part of it acts on the enlarged pressure belt. The compactness of the obtained product is between closed and open pressure. Between the products of the mold, the structure is therefore semi-closed.
When the product is complicated, the semi-closed stamper (compared with the closed stamper) is easy to process, the filler and the take-up product are also convenient, and the feeding amount does not have to be as precise as the closed stamper, but in the pressure belt There is a rubber edge. If the fluidity of the rubber is poor, the rubber edge is thicker, which affects the appearance and dimensional accuracy.
The semi-closed filling mold structure has better exhaust performance, and the density of the product parts is also relatively high, the rubber material loss is small, the utilization rate is high, and the mold opening is convenient. This type of mold is suitable for the molded production of rubber molded parts of the inner fabric.
The mold manufacturing process is better, and the surface roughness of the cavity is easily reduced, which is very advantageous for improving the apparent quality of the product parts.
What is a multi-cavity molding die?
2019年3月3日
Rubber Molds FAQs
Comments Off on What is a multi-cavity molding die?
Editor
The so-called multi-cavity molding die is a mold in which two or more or more than one hundred cavities are designed and manufactured in one set of molds. Design and manufacture multi-cavity molding die, the purpose of which is to improve the production efficiency of molding processing. For small rubber products, the economic benefits are very significant. Multi-cavity molding die, with integral stencil structure, core mold frame structure and replaceable combined structure.